We are a Czech company that operates in the field of modeling, simulation and optimization of production. We focus on the concept of Industry 4.0, such as the design and implementation of innovative PLM products including specialised customization and complex solutions. We also provide related consultations and training. We have our own development department and we are one of the few suppliers capable of complex programming, development of user modules and expansion of Teamcenter and Tecnomatix products. We always try to understand what the customer needs to offer a tailored solution that will not only be fully functional but also user-friendly.
We are a Czech company that operates in the field of modeling, simulation and optimization of production. We focus on the concept of Industry 4.0, such as the design and implementation of innovative PLM products including specialised customization and complex solutions. We also provide related consultations and training. We have our own development department and we are one of the few suppliers capable of complex programming, development of user modules and expansion of Teamcenter and Tecnomatix products. We always try to understand what the customer needs to offer a tailored solution that will not only be fully functional but also user-friendly.
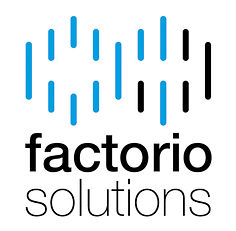-compressor.jpg)
See our portfolio

Stay informed!